The Crucial Role of Bulk Properties in Scaling Chemical Materials for Efficient Mass Production
When developing chemical materials, research and development teams often begin at a small scale. In the early stages, the focus is primarily on the fundamental properties of the material itself, including its molecular structure, its surface area, the nature of its chemical bonding, its morphology, and its intrinsic reactivity. These characteristics are crucial for determining the eventual performance of the material in its intended application, whether that application is as a catalyst, a polymer additive, a coating material, a battery electrode component, or any other specialized function.
The initial development phase involves in-depth analysis using advanced characterization and simulation techniques to thoroughly understand the material’s fundamental properties. This crucial step provides the foundational knowledge necessary for optimizing its performance and ensuring consistent quality during large-scale manufacturing.
However, a significant challenge arises when moving from small-scale laboratory development to larger-scale manufacturing. The material that performed exceptionally under controlled, small-batch conditions may not behave the same way in bulk. In fact, certain properties that were previously negligible or easily managed at the laboratory level can become critically important when the material is synthesized, processed, and handled in ton-scale quantities. Bulk Properties such as viscosity, density, rheology, large-scale particle size distribution, compressibility, thermal stability, and mechanical handling characteristics, including flow properties of powders or slurries, come to the forefront.
Neglecting these considerations in the scale-up phase can lead to unpredictable outcomes, including incomplete reactions, degraded product quality, lower yields, equipment fouling, costly downtimes, and inconsistencies in product properties from batch to batch. Ensuring stable mass production of chemical materials therefore requires a holistic understanding that merges the molecular-level features developed in research and development with the macroscopic factors necessary for large-scale manufacturing. Bulk Properties serve as the bridge connecting these two realms and allow materials to retain their carefully designed functionalities at industrial scales.
Understanding the Fundamental Properties
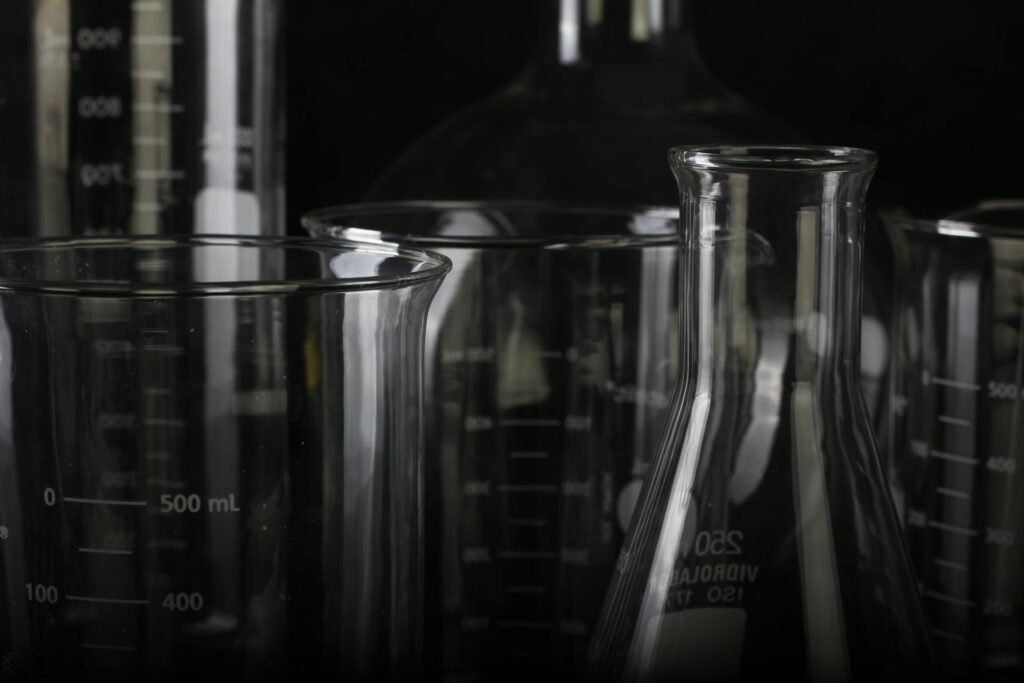
Molecular Structure:
At the root of a chemical material’s characteristics is its molecular structure. This encompasses the arrangement of atoms, chemical bonds, and overall molecular geometry. The structure influences how the material interacts with other substances and whether it can be modified to deliver improved performance. For example, in polymer materials, controlling molecular weight distribution, branching, and the presence of functional side groups can significantly impact glass transition temperature, mechanical strength, and solubility. At the R&D stage, determining the optimal molecular architecture ensures the material meets target performance criteria before considering Bulk Properties at larger scales.
Surface Area and Morphology:
Many chemical materials, especially catalysts, adsorbents, and battery electrode materials, rely heavily on their surface characteristics. A high surface area, finely tuned pore structure, and carefully engineered morphology can influence chemical reactions and the accessibility of active sites. During the laboratory phase, researchers might adjust synthesis parameters such as temperature, pH, solvents, and reaction time to achieve the desired surface area or pore size distribution. The ultimate goal is to provide optimal performance, and later integrating considerations related to Bulk Properties ensures that this performance translates successfully into full-scale production.
Intrinsic Reactivity and Selectivity:
A material’s chemical reactivity, whether in catalytic processes, polymerization reactions, or other functional applications, depends on its active sites and how it interacts with reactants. At the small scale, measuring reaction kinetics and selectivity under controlled conditions is essential. Understanding these intrinsic properties is key to designing materials that deliver high efficiency in their intended roles. Recognizing that Bulk Properties will also influence performance at large scale allows for a more comprehensive design approach.
Particle Size and Morphological Uniformity:
At the bench scale, controlling particle size distribution often involves techniques like precipitation, crystallization, milling, or managing aggregation. Uniform particle size and shape can deeply influence a material’s capabilities. For example, a catalyst powder with narrow particle size distribution ensures consistent diffusion paths and reaction kinetics. Similarly, controlling particle sizes in battery electrode materials affects charging and discharging rates. While these parameters are crucial at the small scale, appreciating that Bulk Properties related to large-scale handling and processing will also emerge is essential for smooth scaling.
The Shift to Bulk Production
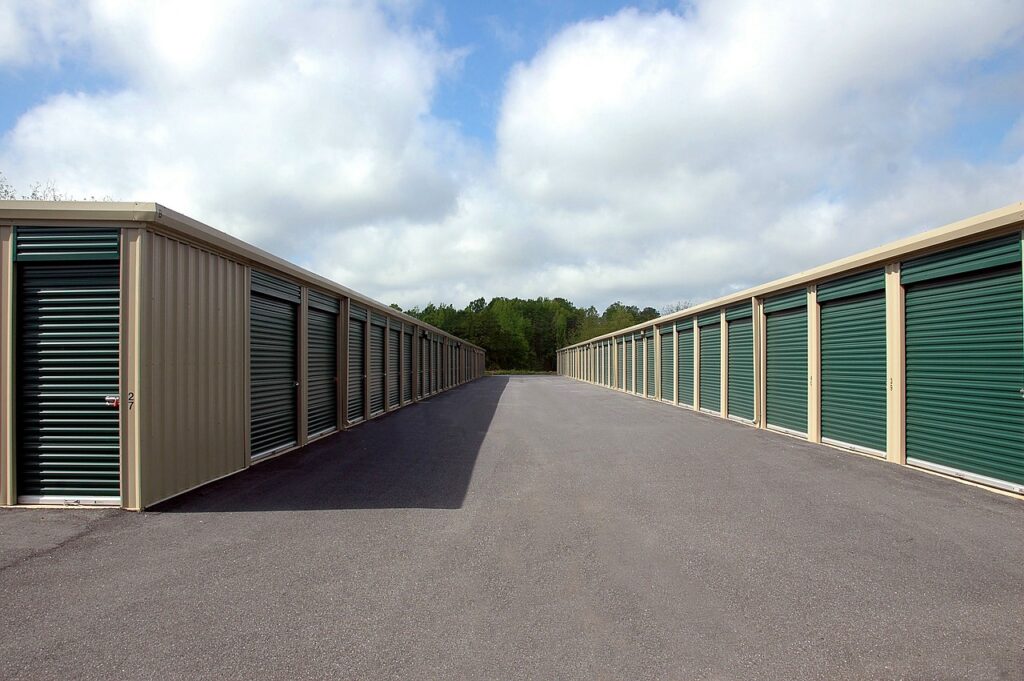
Once these fundamental properties have been fine-tuned and the material shows promise, the next step is scaling up. At this stage, previously invisible considerations take center stage. Producing tens, hundreds, or thousands of kilograms, or even metric tons, shifts the focus from microscopic precision to the macroscopic realm. Bulk Properties define how effectively the material transitions into full-scale manufacturing processes.
Viscosity and Rheology:
Viscosity and rheology exemplify Bulk Properties that may not significantly affect performance at laboratory scale but become vital at industrial volumes. For liquids, suspensions, or slurries, viscosity determines how easily the material can be pumped, stirred, or mixed. High viscosity can slow down processing steps, increase energy consumption, and cause uneven mixing or incomplete reactions. Shear-thinning or shear-thickening behaviors become more pronounced with large agitators and pumps. Understanding these Bulk Properties ensures efficient equipment function and consistent product quality.
Density and Bulk Density:
Density and bulk density are Bulk Properties that influence handling and stability in large-scale operations. Differences in density can affect settling, stratification, and phase separation in large batches. For powders, bulk density determines hopper design, pneumatic transport requirements, and how materials pack into containers. Inconsistent bulk density can complicate metering, blending, and dispensing. Managing these Bulk Properties ensures stable operations and uniform product quality as production volumes rise.
Scale-Dependent Mixing and Mass Transfer Limitations:
In a small laboratory flask, mixing is easily achieved with a simple stirrer. At large scales, mixing presents complex engineering challenges directly linked to Bulk Properties. As reactor volumes increase, achieving homogeneous mixing, avoiding dead zones, and ensuring adequate mass transfer become critical. Diffusion limitations that were negligible at small scale can become major barriers, and heat transfer becomes less efficient. By focusing on Bulk Properties at an early stage, it is possible to avoid temperature gradients, product variations, and unwanted side reactions.
Mechanical Strength, Compressibility, and Handling:
When dealing with bulk solids such as powders or granules, mechanical Bulk Properties must be considered. Will the powder cake in silos or hoppers? How easily does it flow through conveying systems? Does it produce excessive dust or fines, potentially causing quality issues or safety hazards? Addressing these Bulk Properties ensures robust industrial processes and stable product quality throughout packaging, transport, and storage.
Stability Under Industrial Conditions:
Some materials appear stable at the small scale but undergo unexpected changes when produced and stored in bulk. Subtle temperature gradients, humidity, oxygen exposure, and light can alter Bulk Properties over time. Ensuring stability across the entire supply chain, from production to end-user application, requires attention to Bulk Properties that reflect environmental conditions and packaging strategies.
Bridging the Gap: Strategies for Success
Merging molecular-level precision with industrial practicality demands an integrated, forward-thinking approach. Bulk Properties guide us through this process, ensuring that our scaled-up operations yield consistent, high-quality results.
Collaborative Expertise Across Disciplines
Successfully addressing Bulk Properties involves chemists, materials scientists, chemical engineers, mechanical engineers, quality assurance professionals, and operations specialists. Each discipline provides unique insights that, when combined, ensure that microscopic design parameters align with Bulk Properties governing large-scale performance.
Pilot-Scale Testing
Pilot plants serve as valuable intermediates between lab work and full-scale manufacturing. They reveal Bulk Properties that may pose challenges, including viscosity, flow issues, or stability concerns. Testing formulations and equipment configurations at this intermediate scale allows for refinements that save time, resources, and potential frustration later.
Advanced Characterization and Computational Modeling
While molecular-level characterization remains important, studying Bulk Properties requires additional tools. Rheometers, flow testers, and large-scale particle size analyzers help assess critical Bulk Properties. Computational fluid dynamics and discrete element modeling predict how materials behave in large reactors or handling systems, allowing engineers to identify and resolve potential problems before full-scale implementation.
Adjusting Formulations with Additives such as surfactants
Sometimes the ideal microscopic formulation needs slight modifications to optimize Bulk Properties. Adding dispersants, stabilizers, or adjusting molecular architecture can improve flow, reduce viscosity, or enhance stability at scale. By considering Bulk Properties from the start, materials become easier and more cost-effective to produce without sacrificing quality.
Robust Process Control
Full-scale production demands continuous monitoring to maintain product consistency. Automated sensors, online analyzers, and advanced process controls help track Bulk Properties such as viscosity and particle size distribution in real time. This proactive approach preserves the connection between molecular-level design and large-scale manufacturing realities.
Looking Ahead: A More Integrated Future
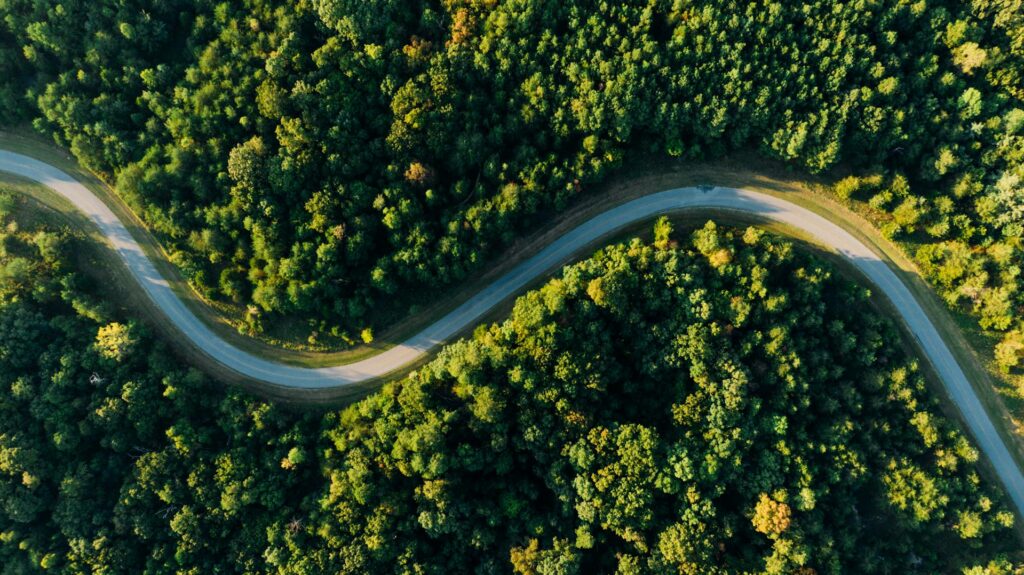
As our understanding of Bulk Properties deepens, designing materials with scalability in mind becomes more natural. This integrated mindset leads to more sustainable, cost-effective, and reliable materials that excel in real-world applications. By embracing Bulk Properties at every stage, we ensure that breakthroughs made in the lab reach their full potential on the global stage.
In the end, acknowledging Bulk Properties and addressing them thoughtfully allows us to achieve stable, high-quality mass production. It enables us to transform laboratory discoveries into impactful, commercially viable solutions. This holistic perspective ensures that the products we create are ready for the challenges of industrial manufacturing and can truly make a difference in the world.
Source: https://thebulklab.com