Next-Generation Materials Laboratory : Innovations in Alloys, Amorphous Materials, and Composites
In the near future, materials laboratory is expected to feature robotic arms meticulously assembling samples, while AI systems simultaneously analyze data in real-time. Such a scene is not merely science fiction; it represents the forthcoming reality of next-generation labs that will revolutionize the way materials—from advanced alloys to sophisticated composite materials—are produced. Approximately a decade ago, the U.S. Materials Genome Initiative challenged scientists to discover and manufacture novel materials twice as fast and at a fraction of the traditional costs. Achieving these ambitious goals has become even more urgent due to climate change, geopolitical tensions, and unstable supply chains.
To realize such accelerated innovations, a paradigm shift in materials laboratory workflow is essential. Future labs will replace slow, isolated experiments with fully integrated, automated pipelines that seamlessly combine design, synthesis, processing, and characterization. Utilizing next-generation experimental tools, automation, AI and machine learning integration, and multimodal characterization, these labs aim to quickly bridge the gap from material invention to practical production technologies. These advancements address critical bottlenecks in the manufacturing of metal alloys, amorphous materials (such as glasses), and composites, significantly impacting future manufacturing strategies.
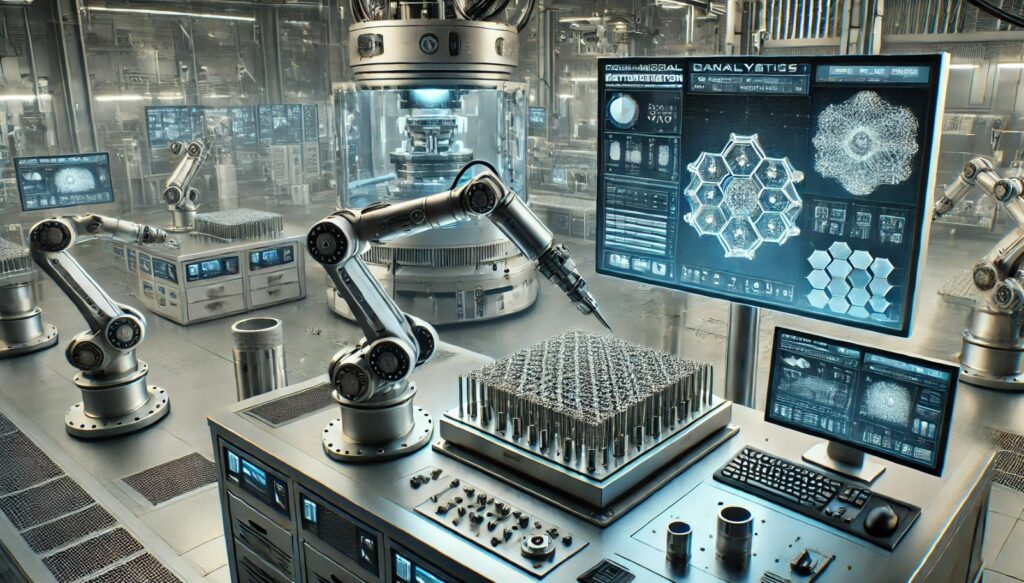
Key Innovations Enabling Future Materials Laboratory
Firstly, autonomous AI-driven experimentation involves robots and machine learning algorithms collaboratively planning, executing, and analyzing experiments, thereby maximizing speed and efficiency. Secondly, high-throughput alloy libraries and sample arrays enable simultaneous exploration of diverse material compositions and structures within a single production batch, revolutionizing the pace of new material discovery. Thirdly, multimodal and multiscale characterization technologies use advanced microscopy and sensors—including synchrotron X-rays and cryogenic electron microscopy (Cryo-EM)—to precisely examine material properties from atomic to macroscopic scales, with AI managing and interpreting vast amounts of data. These innovations swiftly close the gap between material development and manufacturing, making lab discoveries quickly translatable to real-world industrial applications.
Alloys: High-Speed Synthesis and Testing
In futuristic materials labs, robotic arms collaborate with laser-based 3D printers to swiftly produce and evaluate various alloy samples. Traditional alloy development typically involves extensive time-consuming explorations of compositions, phase ratios, and microstructures. Conventional manufacturing processes usually optimize a single alloy composition per batch, limiting development speed. Next-generation labs completely transform this approach by creating “alloy libraries,” generating multiple compositions and microstructures simultaneously within a single batch.
For instance, laser-directed energy deposition (L-DED), a metal 3D printing method, produces a single metallic sample with a gradient composition along its length. By applying temperature gradients or different stresses across various regions of this graded sample, all conditions can be simultaneously evaluated, eliminating the need for separate experiments. One recent study successfully measured oxidation rates across an entire gradient alloy sample in a single experiment, illustrating how numerous alloy compositions can be screened simultaneously. Integrating automation and AI data analysis can reduce alloy development timelines from years to mere weeks, significantly simplifying the transition from lab discovery to industrial production.
Amorphous Materials: Real-Time Atomic-Level Insights
Amorphous materials like glasses, metallic glasses, and polymers exhibit atomic arrangements that are inherently disordered, making their behavior challenging to predict. Atoms within these materials constantly rearrange themselves over vast spatial and temporal scales, presenting significant challenges to researchers. New experimental techniques now allow scientists to observe atomic motion in real-time. Methods such as X-ray photon correlation spectroscopy (XPCS) and electron correlation microscopy (ECM) utilize coherent beams to capture dynamic local movements within glass or liquid structures.
For example, XPCS experiments revealed that silica glass, even far below its glass transition temperature, displayed unexpectedly rapid structural relaxation in microscopic regions, behaving like liquid pockets within a solid. These discoveries enhance our understanding of amorphous materials, though they generate enormous volumes of data. Each experiment can yield terabytes of data, making human analysis impractical. Consequently, AI and machine learning have become essential tools in materials laboratory, sifting through noisy data to identify meaningful patterns and correlate atomic-scale events with bulk properties. Real-time feedback from such advanced experiments could enable precise control over amorphous materials, facilitating the creation of glass displays resistant to aging or bulk metallic glasses with adjustable flexibility.
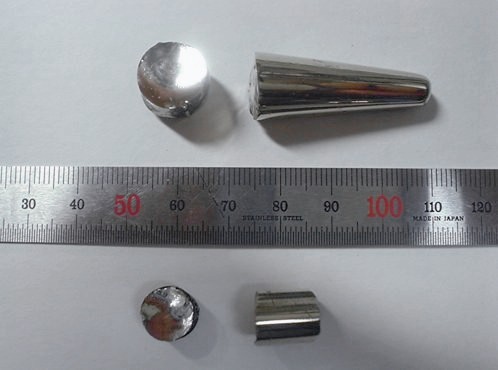
Composites: Observing Hidden Interfaces via Cryo-EM
Researchers now use cryogenic electron microscopy (Cryo-EM) to observe delicate interfaces within composite materials, critical in applications ranging from battery electrodes to biomedical implants. Composite interfaces often determine overall performance yet are challenging to observe due to their softness and moisture content, which complicate traditional electron microscopy.
Combining Cryo-EM with focused ion beam (FIB) milling addresses this challenge. Samples are rapidly frozen, then milled into ultra-thin sections at low temperatures, allowing observation of fragile interfaces in near-natural conditions. For example, Cryo-EM analysis of next-generation lithium metal batteries revealed two distinct dendritic structures forming from the anode, each with unique morphology and composition, critical for enhancing battery safety and longevity. Cryo-EM similarly sheds light on processes such as nanoparticle crystallization within soft matrices and mineral nucleation in biological tissues.
Insights from these investigations provide engineers with essential guidance on improving composite materials—whether by tweaking interface chemistries to prevent corrosion or designing nanoscale reinforcements to enhance strength. As Cryo-EM and multimodal analytical techniques become standard tools, and AI assists in image analysis, engineers will rapidly identify failure mechanisms and optimize interfaces in real-time. This reduces manufacturing blind spots, enabling more confident scaling of composite designs from lab development to industrial application.
The Future of Next-Generation Materials Laboratory
From aerospace alloys to flexible display glasses, advancements in materials laboratory promises to significantly shorten the journey from discovery to production. Notably, elements of this future are already becoming reality. For instance, researchers at Argonne National Laboratory have developed Polybot, an autonomous laboratory system leveraging AI robotics to rapidly optimize new materials. As such automated, data-driven approaches spread, production engineers can anticipate an era where materials R&D becomes a responsive innovation partner rather than a bottleneck.
(Video by Argonne National Laboratory.)
Current creative solutions pioneered for alloys, amorphous materials, and composites suggest a future where rapid advancements in bulk materials keep pace with dynamic technological demands, rapidly turning laboratory breakthroughs into practical, market-ready products.
DOI: https://doi.org/10.1557/s43577-024-00846-y
Source: https://thebulklab.com