The Unseen Engine: How Roll to Roll Coating is Powering the Future of Energy and Electronics
1. Introduction: The Quiet Revolution of Roll to Roll Manufacturing
Modern technological advancements, from the ubiquitous smartphone to the burgeoning electric vehicle market, rely on sophisticated manufacturing processes that can produce high-performance components with incredible efficiency. At the forefront of this industrial evolution is roll to roll (R2R) coating, a continuous, high-efficiency manufacturing method. This process involves applying various fluid materials onto flexible substrates, such as plastic films, metal foils, or even paper, as they are seamlessly fed from one large roll to another. This technique has become an indispensable tool for creating multi-layered sheet-type products that are fundamental to today’s innovations.
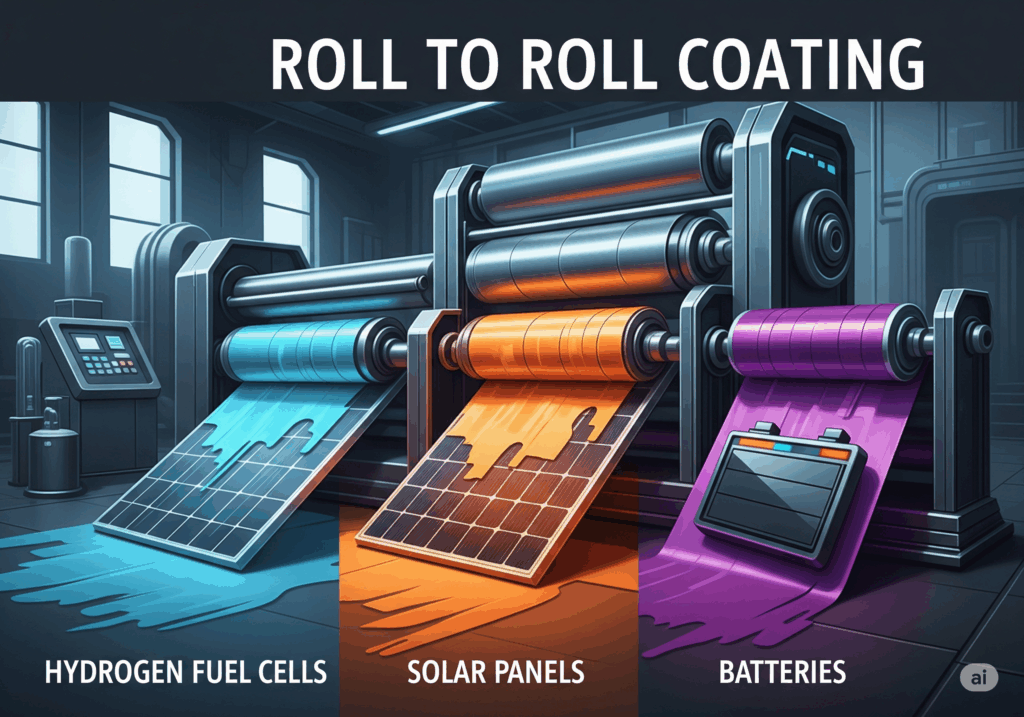
The increasing prominence of R2R coating is particularly pronounced in high-growth sectors like solar cells and batteries. In these industries, the demand for precision, scalability, and cost-effectiveness is paramount. The inherent ability of R2R to handle large volumes of material while maintaining consistent quality makes it a cornerstone technology for the future of energy generation and storage, as well as for advanced electronics. The continuous nature of R2R operations directly translates into significant gains in efficiency and scalability, offering a fundamental economic advantage over traditional batch processes. This capability is the primary economic driver behind its widespread adoption and sustained growth, enabling manufacturers to meet the escalating global demand for flexible and energy-related products effectively.
2. Demystifying Roll to Roll Coating: Process and Precision
At its operational core, R2R coating orchestrates a continuous flow of material. A flexible substrate is unwound from a supply roll, meticulously guided through a series of integrated processing stations—which can include surface preparation, coating application, drying or curing, and in-line inspection—before the finished product is precisely rewound onto another roll.1 This seamless, uninterrupted operation is designed to minimize production downtime and maximize throughput, yielding significant manufacturing advantages.
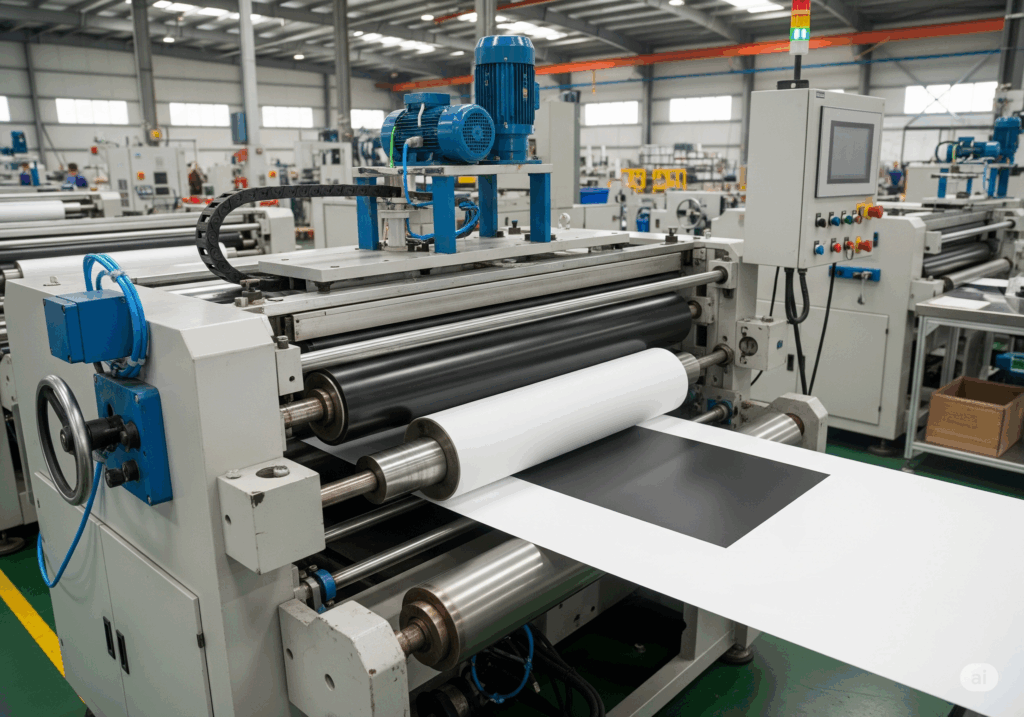
Ke – y Coating Techniques
Within the R2R framework, various coating techniques are employed, each suited to specific material properties and desired film characteristics:
- Slot-Die Coating: This highly precise, pre-metered method is a cornerstone of advanced R2R applications. It involves dispensing a uniform film of coating material through a narrow, precision-machined slit directly onto the moving substrate. This technique offers exceptional control over wet film thickness and coating width, even at high web speeds, and significantly minimizes material waste due to its pre-metered nature. It is particularly favored for applying expensive or sensitive formulations, such as nanoparticle suspensions, perovskite inks, or polymer blends, where material efficiency and layer uniformity are critical.
- Gravure Coating: This method utilizes a patterned roller (gravure cylinder) to pick up and transfer coating material onto the substrate. It is ideal for creating intricate designs, textured coatings, or applying very thin, consistent layers at high speeds.
- Roll Coating: A versatile category that employs a series of plain rollers to meter and apply liquid. Configurations like the three-roll reverse coater are widely used for their high precision, often preferred for low to medium viscosity resins to produce smoother, more stable films. Two-roll reverse coaters are also common, particularly for optical functional materials or resins containing fillers. This broad category accommodates a wide range of viscosities and film thicknesses.
- Other Methods: Additional techniques include knife-over-roll coating, which controls thickness with a blade, and dip coating, where the substrate is submerged in the coating solution.
Ensuring Quality and Uniformity
The success of R2R coating hinges on meticulous control over several critical parameters to ensure superior product quality and uniformity:
- Web Tension Control: Maintaining constant and uniform tension on the flexible substrate as it moves through the system is paramount. Deviations in tension can lead to defects such as wrinkles, misalignment, and inconsistent coating thickness, directly impacting the final product’s integrity and performance.
- Drying and Curing: Following coating, the substrate passes through specialized drying or curing systems, which may utilize heated air ovens, infrared (IR) heaters, or ultraviolet (UV) curing systems. This step is crucial for removing solvents or solidifying the applied material, preventing defects like bubbles, cracks, or non-uniformity.
- Precision Control of Parameters: Achieving the desired coating thickness and uniformity requires precise control over factors such as the rotation speed of the rollers, the substrate speed, the rheological properties of the coating fluid (e.g., surface tension, viscosity, density), the coating gap (distance from the die to the substrate), and the alignment of the coating head with respect to the moving web. The ability to achieve uniform coating thickness and quality through these precise methods is the technical foundation for high-performance applications. This level of precision is essential for functional materials where even micron-level deviations can significantly impact device performance, such as in advanced batteries and solar cells.
The entire R2R process, from the initial unwinding to the final rewinding, functions as a tightly integrated system. Each individual step—from surface preparation and coating application to drying, quality control, and tension management—profoundly influences the quality of the final product. A defect or inconsistency introduced at any stage can propagate throughout the continuous web path, compromising the entire production run. Therefore, optimizing R2R is not about isolated improvements but about holistic system integration and control, where every variable in the continuous chain is meticulously managed.
The pre-metered nature and high precision of slot-die coating make it uniquely suitable for handling expensive and sensitive advanced materials, such as perovskite inks and nanoparticle suspensions. This minimizes material waste and ensures consistent performance, positioning slot-die as a critical enabler for the development and mass production of next-generation energy and electronic devices.
Table 1: Key Roll to Roll Coating Methods and Their Characteristics
Method | Principle | Key Advantages | Typical Applications |
Slot-Die Coating | Pre-metered, precise dispensing through a slit onto moving substrate. | High precision, minimal material waste, excellent layer uniformity, compatibility with multilayer coating, thin layers (sub-micron). | Flexible printed circuits, OLED displays, thin-film batteries, perovskite solar cells, advanced functional films. |
Gravure Coating | Uses a patterned roller to transfer coating material. | Intricate designs, textured coatings, high-speed, high versatility. | Printing and graphics, decorative films, security features, patterned electrodes. |
Roll Coating (e.g., Three-Roll Reverse) | Meters and applies liquid via a series of rotating rolls, often with reverse metering. | High precision, suitable for various viscosities (low to high), thin to thick films, stable film formation. | Adhesives, optical functional materials, resins containing fillers, general industrial coatings. |
Knife-over-Roll Coating | Controls coating thickness with a blade over a support roll. | Simple configuration, good for thicker coatings, cost-effective. | Medical films, adhesive tapes, barrier films. |
Dip Coating | Submerges the substrate in a coating solution, removing excess material. | Simple, suitable for complex shapes, uniform coating on both sides. | Medical diagnostic strips, protective coatings, functional membranes. |
III. The Expanding Reach: Current Applications and Market Dynamics
Roll to roll coating has established itself as a cornerstone technology across a multitude of industries, a testament to its inherent efficiency, versatility, and ability to deliver high-quality products at scale.
Diverse Industrial Applications
The R2R process is integral to the manufacturing of a wide array of advanced products:
- Energy Storage: R2R is crucial for manufacturing flexible printed circuits, OLED displays, and thin-film batteries. It is extensively used for coating electrodes and separators in lithium-ion batteries and supercapacitors, which are vital components in electric vehicles and portable electronics.
- Renewable Energy: The technology is essential for the high-volume production of photovoltaic films, flexible solar panels, and emerging perovskite solar cells, contributing significantly to the global shift towards sustainable energy solutions.
- Flexible Electronics & Displays: R2R is fundamental in creating flexible printed circuits, OLED displays, and e-paper. It also plays a key role in producing transparent conductive films (TCFs) for touchscreens, enabling the development of bendable and lightweight electronic devices.
- Packaging: In the packaging industry, R2R coating applies barrier films that offer protection against moisture, gas, or light. It is also used for creating security features like holographic films and tamper-evident labels, enhancing product integrity and brand protection. This capability moves packaging beyond simple containment, adding significant value by providing advanced functionalities that impact brand protection and consumer safety.
- Healthcare: The R2R process is vital for coating medical films, adhesive tapes, and diagnostic test strips. It enables the production of flexible sensors for wearables and microfluidic devices, supporting advancements in personalized medicine and remote patient monitoring.
- Smart Textiles: R2R technology is enabling the integration of conductive paths into e-textiles and functional clothing. This allows for the creation of smart garments with embedded sensors for monitoring vital signs or even generating power from movement, opening new frontiers in wearable technology.
Market Growth and Drivers
The global R2R coating machine market is experiencing robust growth, driven by several interconnected factors. The increasing adoption of flexible electronics, coupled with continuous advancements in renewable energy technologies and the escalating demand for high-quality, cost-effective packaging solutions, are key contributors to this expansion.
The market size was valued at USD 981.1 million in 2024 and is projected to reach USD 1,029.18 million in 2025. This growth trajectory is expected to continue, with the market expanding to USD 1,509.03 million by 2033, demonstrating a Compound Annual Growth Rate (CAGR) of 4.9% during the forecast period of 2025–2033. This robust growth is not merely organic; it is fundamentally fueled by the increasing adoption of high-tech flexible electronics, the global imperative for renewable energy, and the industry’s growing focus on sustainable manufacturing processes. This indicates a strong, long-term market demand and a fundamental shift towards greener, more efficient industrial practices, ensuring R2R’s continued relevance and attracting significant investment.
Key drivers for this market expansion include the global push for renewable energy, which fuels demand for high-volume R2R coating of photovoltaic cells, and continuous innovation in coating technologies, which enhances speed, precision, and efficiency. Furthermore, increasing automation and digitalization, including the integration of AI and robotics, are gaining momentum, improving production speed and quality control. Geographically, East Asia, particularly China, South Korea, and Japan, holds the largest market share. This dominance is attributed to the region’s strong electronics manufacturing base and large-scale solar energy installations. This geographical concentration highlights that a significant portion of R2R innovation, manufacturing capacity, and market demand is centered in this region, profoundly influencing global supply chains and competitive landscapes in high-tech manufacturing.
The ability of R2R, especially when paired with slot-die technology, to efficiently and cost-effectively scale up material and device technology from laboratory research to pilot and full production is a critical factor in its widespread adoption. This means that R2R equipment manufacturers are not merely selling machinery; they are enabling the commercialization of cutting-edge research, accelerating the transition of scientific discoveries into marketable, real-world products.
Table 2: Global Roll-to-Roll Coater Market Snapshot (2024-2033)
Category | 2024 Value | 2025 Value | 2033 Forecast | CAGR (2025-2033) |
Market Size (USD Million) | 981.1 | 1,029.18 | 1,509.03 | 4.9% |
Dominant Region | East Asia (China, South Korea, Japan) | East Asia (China, South Korea, Japan) | East Asia (China, South Korea, Japan) | N/A |
Key Application Segments (2023 Share/Growth):
- Displays and Panels: Largest segment, accounting for over 51% of global flexible OLED displays and touchscreens.
- Automotive: Growing steadily, with 26% of advanced driver-assistance system (ADAS) hardware incorporating R2R-coated transparent conductive films.
- Packaging and Labels: Significant growth, with flexible food-grade packaging films coated with R2R aluminum and oxygen barrier layers growing by 31% in Asia-Pacific.
4. Global Innovators: Leading Roll to Roll Equipment Manufacturers
TThe global R2R equipment market is mainly led by Asian companies, with major players from North America and Europe participating. Each company contributes its own expertise and technological advancements.
1) Hirano Tecseed (Japan)
Hirano Tecseed is a prominent Japanese manufacturer recognized for its extensive range of coating solutions. Their product portfolio includes versatile Roll Coaters, adaptable for various viscosities and speeds, and specialized Three Roll Reverse coaters designed for high-precision applications with relatively low viscosity resins. They also offer Two Roll Reverse coaters, frequently utilized for optical functional materials and resins containing fillers. Beyond these, Hirano provides Comma, Closed Type, Die, and Gravure coaters, complemented by advanced drying systems.
Hirano is strategically investing in digitalization and advanced simulation technologies to enhance its manufacturing processes. The company has partnered with Siemens to develop a “digital twin” of its battery manufacturing equipment. This virtual replication allows Hirano to optimize web handling, predict potential defects, and significantly reduce the time to market for new products. This capability enables virtual testing and a five-times faster evaluation of new materials and machine parameters compared to physical trials. This strategic focus on advanced manufacturing optimization positions them at the forefront of innovation in both process efficiency and new material applications. Furthermore, Hirano is actively developing new coating equipment specifically for perovskite solar cells, a next-generation photovoltaic technology. Detailed specifications for this new equipment are planned for January 2025, with a prototype exhibition in January 2026, and the first unit delivery anticipated in May 2026. This clear roadmap for perovskite solar cell technology underscores their commitment to emerging renewable energy solutions.
2) SFA (South Korea)
SFA is a major South Korean player providing comprehensive solutions for the secondary battery industry. The company offers total turnkey solutions that encompass automated logistics systems, manufacturing equipment, and inspection/measurement tools across all stages of secondary battery production, from raw materials to finished products. While specific details on their direct R2R coating machines are less elaborated in the provided information, their involvement in “Roll to Roll wet Process equipment in the FPD (Flat Panel Display) manufacturing” is noted. Their solutions for battery production include high-performance stacker cranes for aging electrodes, Roll OHT (overhead transport) systems for efficient material movement on battery cell production lines, and oven stockers for automated loading and unloading of rolls into ovens. SFA’s strength lies in providing comprehensive solutions for the entire secondary battery production process, encompassing not just coating but also logistics, process equipment, and inspection. This signifies a holistic approach to factory automation, which is critical for meeting the high-volume demands of the electric vehicle battery market. SFA’s focus on “Smart Factory” solutions, which integrate AI and route optimization technology, indicates a strong push towards advanced automation and data-driven manufacturing processes. This approach is designed to enhance overall efficiency and quality in battery production, aligning with industry trends towards intelligent manufacturing.
3) PNT (South Korea)
PNT, or People & Technology, is recognized as a world-class expert in R2R converting machinery, with a particular specialization in equipment for secondary batteries. Their core offerings include Electrode Coaters designed to apply and dry lithium-ion battery active materials onto aluminum and copper foils. These coaters boast impressive production speeds, capable of reaching up to 100 m/min with sequential double-sided coating, achieved through dry chambers up to 80 meters long. PNT also manufactures Electrode Roll Presses for precise thickness control of coated webs, ensuring reproducibility within 1µm through a hydraulic servo control system. Additionally, their Electrode Slitters accurately cut coated or non-coated parts of the rolled electrode to desired widths, incorporating block knife cartridge units for precision and foreign body prevention measures.
PNT’s deep specialization and patented dry coating technology position them as a leader in high-productivity, sustainable battery electrode manufacturing. The company has secured a patent for a revolutionary dry electrode double-side coating technology for EV batteries. This innovation fundamentally addresses key industry challenges by eliminating the need for toxic solvents and energy-intensive drying processes, which significantly reduces energy consumption by up to 46% and manufacturing costs by nearly 19% compared to traditional wet coating methods. This dry coating technology also enhances microstructural uniformity, leading to improved electrochemical performance and cycle stability of batteries. The unique “L” shaped roller arrangement and precise control systems of this technology underscore PNT’s commitment to sustainable and cost-effective battery manufacturing, offering a significant competitive advantage in the global market.
4) Dürr Systems, Inc. (USA)
Dürr Systems is a prominent system integrator and manufacturer based in the USA, offering comprehensive, turnkey solutions for lithium-ion battery and vehicle manufacturing. Dürr provides complete packages for electrode coating, encompassing both wet and dry coating solutions. Their X.Cellify system enables simultaneous two-sided coating with a straight-path product flow and utilizes air flotation drying, which minimizes edge curl and reduces the required factory floor space. They also offer tandem coating, a mature technology optimized for large foil widths. Dürr’s capabilities extend across the entire production line, including raw material handling, slurry mixing, web handling, calendering, and integrated solvent recovery and purification systems. These systems are designed to capture over 99% of NMP (N-Methyl-2-pyrrolidone), a common solvent, significantly reducing waste and operating costs.
Dürr’s offerings of both wet and dry coating solutions for battery electrodes, coupled with integrated solvent recovery and a strong emphasis on reducing costs and environmental impact, demonstrate a strategic alignment with the battery industry’s critical sustainability goals. This positions them as a key enabler for greener battery production. For future development, Dürr focuses on providing customer-specific process development trials, which dramatically reduce the period between commissioning and full production. They offer LabCoaters for internal product and process development and operate in-house pilot coating lines, indicating a strong commitment to supporting their clients’ R&D efforts and accelerating innovation.
5) FOM Technologies (Denmark)
FOM Technologies, based in Scandinavia, is a provider of high-quality R2R slot-die coating machines. Their product line spans from lab-scale benchtop coaters, such as the FOM omicronR2R, to industrial-scale systems. These machines are characterized by their modular and compact design, offering multiple drying options including infrared (IR), ultraviolet (UV), and hot air. They feature intuitive coating software and precise parameter control, supporting a broad range of material viscosities. FOM Technologies also provides remote support for their equipment.
FOM Technologies’ equipment is specifically designed to support cutting-edge research and development in a wide array of emerging clean energy and electronics applications. This includes 3rd generation solar cells, OLEDs, electrochromic devices, fuel cells, batteries, sensors, membranes, printed electronics, and medical diagnostics. The modular design of their machines allows for seamless adaptation to evolving research needs, effectively safeguarding investment by future-proofing setups as new research directions emerge and technologies develop. This focus on R&D enablement positions FOM as a key partner in accelerating the development of new functional materials and devices.
5. Future Directions and Emerging Applications
The trajectory of roll-to-roll coating technology is marked by continuous innovation, driven by the increasing demand for high-performance, cost-effective, and sustainable manufacturing solutions across diverse sectors.
Advancements in Core Technology
Future developments in R2R coating will focus on enhancing precision, speed, and versatility. This includes:
- Enhanced Automation and Digitalization: The integration of robotics, artificial intelligence (AI), and advanced process control systems will become more pervasive. This will enable real-time monitoring, automatic adjustments, and predictive maintenance, leading to improved production speed, quality control, and overall efficiency. Companies like Hirano are already leveraging digital twin technology to optimize web handling and predict defects virtually, significantly reducing development cycles.
- Sustainable Processes: There is a strong industry-wide push towards developing eco-friendly coating materials and reducing energy consumption. Innovations like dry coating techniques, exemplified by PNT’s patented technology, eliminate the need for toxic solvents and energy-intensive drying, leading to substantial reductions in energy use and manufacturing costs. This shift aligns with global sustainability goals and offers a cleaner, leaner production model for batteries and other coated products. Dürr Systems also emphasizes integrated solvent recovery systems that capture over 99% of NMP, further contributing to environmental responsibility and cost savings.
- Multi-layer and Complex Structures: The ability to precisely deposit multiple layers, sometimes down to sub-micron levels, will continue to improve. This is crucial for advanced applications like flexible solar cells, multi-functional displays, and high-density energy storage devices. Research is also exploring the use of paper as a flexible substrate and separator in batteries, which could enable fully disposable and resource-efficient paper-based electrodes.
Expanding Application Horizons
Beyond their established roles in solar cells and batteries, R2R coating is poised to revolutionize several other critical sectors:
- Fuel Cells and Hydrogen Production: R2R manufacturing is gaining significant traction in the production of key components for hydrogen fuel cells and electrolyzers. These devices convert hydrogen and oxygen into electricity (fuel cells) or split water to produce hydrogen (electrolyzers). The process is ideal for coating active materials onto flexible underlayers for electrodes and catalyst films, accelerating commercialization by enabling high-throughput, cost-effective production. Research efforts, such as those by the Roll-to-Roll Consortium at Oak Ridge National Laboratory (ORNL), are focused on scaling up fuel cell and electrolyzer catalysts and optimizing the entire manufacturing process to reduce costs and waste. Microgravure and slot-die coating methods are proving effective for producing high-quality membrane electrode assemblies (MEAs) for polymer electrolyte membrane (PEM) fuel cells, with ongoing research to improve drying strategies and ink formulations.
- Wearable Technology and Medical Devices: R2R is transforming the creation of flexible printed electronics for healthcare. It enables the production of thin, flexible sensors and circuits for medical wearables like smart patches that monitor vital signs (heart rate, glucose levels) and transdermal drug delivery patches. The process allows for high-resolution printing of electrodes and the seamless integration of microelectronics (e.g., Bluetooth chips) onto flexible substrates, making advanced monitoring technologies more accessible and affordable.
- Smart Packaging: R2R coating enhances packaging by applying advanced barrier layers for moisture, gas, or light protection, extending shelf life for food and pharmaceuticals. It also facilitates the integration of printed sensors for smart packaging applications, such enabling real-time monitoring of product conditions or providing tamper-evident features.
- Advanced Materials Manufacturing: R2R is crucial for the scalable production of innovative materials, including conductive inks, barrier films, adhesives, and active layers for energy devices. It is particularly valuable for precise application of sensitive formulations like nanoparticle suspensions and perovskite inks, minimizing waste and ensuring consistent performance. The technology supports the creation of flexible building-integrated photovoltaics (BIPV), e-textiles with conductive paths, and smart windows that can self-adjust optical properties.
6. Conclusions
Roll to roll coating stands as a pivotal manufacturing technology, continuously evolving to meet the demands of a rapidly advancing technological landscape. Its inherent advantages of high efficiency, scalability, and precision have made it indispensable across a broad spectrum of industries, from energy storage and renewable energy to flexible electronics, packaging, and healthcare. The ability of R2R to transition laboratory innovations to mass production, particularly through techniques like slot-die coating, is accelerating the commercialization of cutting-edge materials and devices.
Leading equipment manufacturers, such as Japan’s Hirano Tecseed and South Korea’s SFA and PNT, alongside Western counterparts like Dürr Systems and FOM Technologies, are driving this evolution. Their strategic investments in digitalization, sustainable dry coating technologies, and comprehensive turnkey solutions are not merely incremental improvements; they represent fundamental shifts towards more efficient, environmentally friendly, and intelligent manufacturing processes. The market’s robust growth, particularly in East Asia, underscores the global recognition of R2R’s critical role.
Looking ahead, R2R technology will continue to expand its influence into new frontiers, notably in the scalable production of fuel cells and hydrogen technologies, advanced wearable devices, and smart textiles. The ongoing integration of AI, robotics, and advanced process controls will further refine its capabilities, enabling even greater precision and reducing waste. As industries globally strive for higher performance, lower costs, and enhanced sustainability, roll-to-roll coating will remain an unseen yet powerful engine, quietly revolutionizing how the products of tomorrow are made.
Source: https://thebulklab.com