Bridging the Gap: Scaling Up Wet Milling from Lab to Production
Scaling up a wet milling process from a small laboratory setup to full-scale production is a notorious challenge in industries like ceramics, battery materials, and metal oxides. Many researchers and engineers have experienced the frustration of achieving a perfect powder particle size distribution (PSD) in the lab, only to see it deviate when the process is translated to the factory floor.
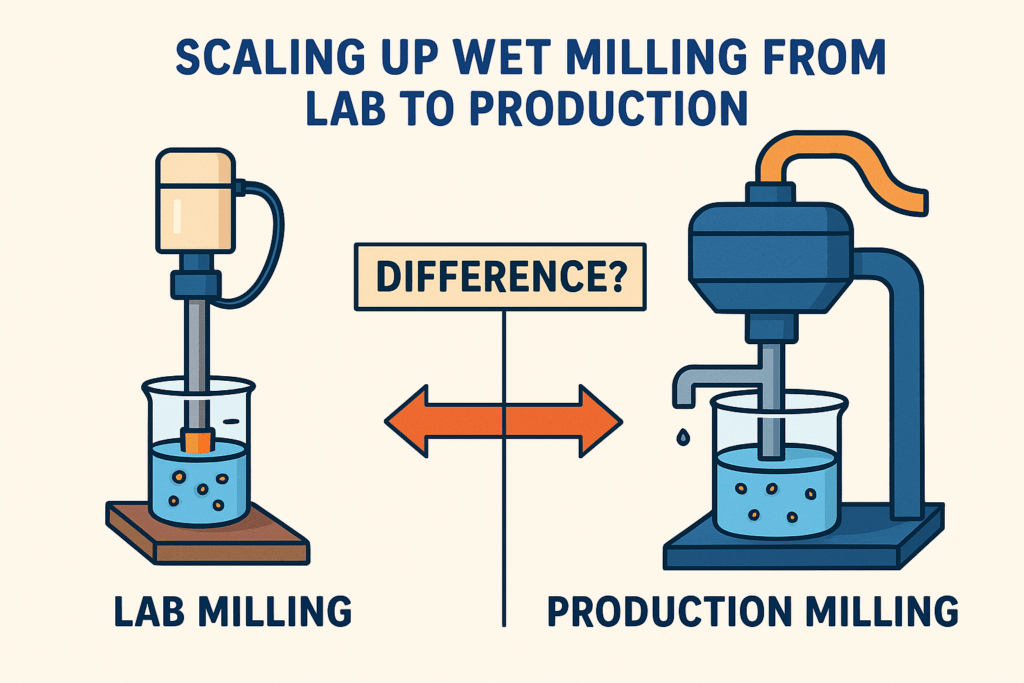
In this article, we’ll explore why that happens and discuss the technology innovations enabling successful scale-up of wet milling – ensuring that powders milled at production scale have virtually the same PSD as those from the lab. We’ll focus on how recent breakthroughs allow us to map lab-scale controls to production conditions effectively, reducing trial-and-error and saving time and resources in the scale-up journey.
The Challenge of Lab to Production Scale-Up in Wet Milling
Wet milling (or wet grinding) is a process where particles are dispersed in a liquid and broken down via mechanical forces. It’s widely used to produce fine powders for ceramics (e.g. alumina, zirconia), battery electrodes (cathode and anode materials), and various oxides and pigments. Wet milling can achieve extremely fine particles with narrow size distributions, which are crucial for product performance. For example, the particle size distribution of battery active materials strongly influences battery capacity, power density, and cycle life. Similarly, in ceramics, a uniform fine powder ensures consistent sintering and material properties.
Scaling up means taking a milling process that works in a beaker or a small lab mill and running it on equipment handling dozens or hundreds of liters. This is easier said than done. Laboratory mills (like small ball mills, bead mills, or high-shear mixers) often operate under conditions that simply can’t be replicated directly in large industrial mills. As a result, when you increase the batch size by 100x or 1000x, you often get different PSDs, unless careful adjustments are made. Key factors such as temperature, milling time, slurry solid content, input energy (RPM or tip speed), and media size all behave differently at scale.
Why Lab and Production Mills Behave Differently
Lab mills and production mills differ significantly, leading to variations in powder particle size distribution when scaling up. Laboratory equipment is smaller, allowing more efficient mixing, better temperature control, and higher energy input relative to its size. In contrast, production-scale equipment is larger, making uniform mixing and heat control challenging. Additionally, the milling speed and energy per unit volume in large mills cannot directly match lab conditions due to mechanical constraints.
Lab setups often optimize solid content and viscosity more easily, while production mills struggle with consistent slurry conditions. Finally, equipment wear in production facilities also contributes to differences in particle size outcomes. These variations explain why direct scale-up from lab conditions often requires careful adjustments to achieve consistent production results.
Innovations That Enable Effective Scale-Up
A critical challenge in the materials industry is maintaining a consistent particle size distribution when scaling wet milling processes from laboratory to mass production. One groundbreaking solution is an automated data-driven approach leveraging digital twin technology, which accurately aligns lab-scale milling outcomes with large-scale production equipment. This method involves systematically collecting milling equipment data (such as milling RPM, duration, temperature, solid content, equipment geometry, and size) alongside resulting powder particle size distributions (PSD, measured as D10, D50, D90, D99) from laboratory experiments.
These comprehensive datasets are fed into advanced algorithms, building predictive models—digital twins—that replicate the milling behavior precisely. These digital twins serve as virtual replicas of both the laboratory and production equipment, enabling users to visualize and analyze the milling process without physically operating the equipment.
When scaling up, the digital twin incorporates production equipment-specific details such as mill volume, agitator type, media size, vessel geometry, and heat dissipation capabilities. The system then automatically predicts and adjusts necessary operational parameters—such as milling speed, milling duration, energy input, slurry viscosity, and cooling conditions—to match lab-scale PSD results. Through continuous machine learning, the model improves its accuracy with every additional dataset, effectively minimizing discrepancies between lab and production outcomes. The substantial benefit of this technology lies in reducing iterative trial-and-error approaches that traditionally consume extensive resources and time.
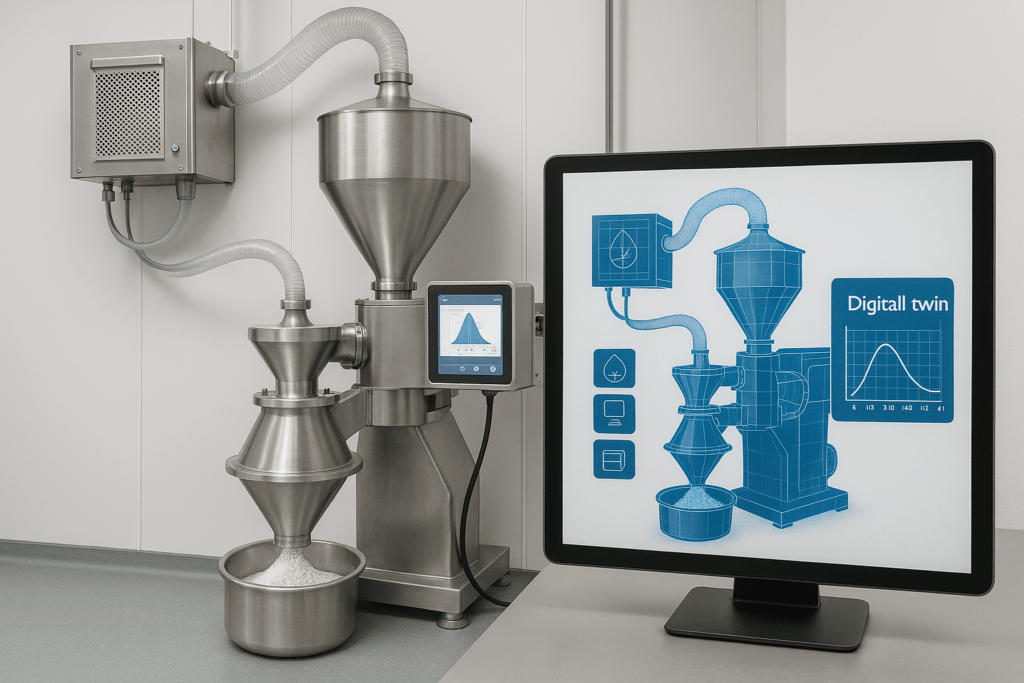
Companies employing digital twin technology have reported significantly decreased lead times and improved consistency in final product quality, as they quickly achieve target particle sizes at scale, preserving critical material properties for industries such as advanced ceramics, battery materials, and oxide manufacturing. This approach also significantly cuts costs associated with material waste, energy consumption, and prolonged equipment downtime. Ultimately, the digital twin-enabled automated matching of powder PSD revolutionizes scale-up technology, providing intuitive, efficient, and accurate transitions from laboratory discoveries to industrial-scale production.
Examples of platforms and technologies supporting these digital twin methods include Siemens’ comprehensive digital twin solutions, Ansys Twin Builder for physics-based predictive modeling, AspenTech’s digital twin platform tailored for chemical and material process optimization and GE Digital’s advanced industrial-scale predictive digital twin solutions. These advanced tools equip industry professionals to confidently scale-up milling processes, transforming complex powder particle size control into a simplified, reliable, and repeatable engineering workflow.
Benefits of Modern Scale-Up Technology
Implementing these innovations in scale-up of wet milling offers substantial benefits:
- Time Savings: Perhaps the biggest win is time. A well-designed scale-up process can shave months off a production launch. Instead of repeated trial-and-error runs, you can often dial in the conditions in just one or two trials. As one equipment maker noted, “previous trials will help expedite the validation process, minimizing downtime before production can begin”. Faster scale-up means faster time-to-market for new products.
- Reduction in Wasted Materials: Each failed trial at production scale can waste hundreds of kilograms of material (which may be expensive battery cathode powders or specialized ceramics). By scaling up right the first time, you dramatically reduce scrapped batches and raw material costs. Better yet, you don’t have to sacrifice large amounts of material in testing – you either use small pilot quantities or rely on simulation, preserving resources.
- Consistency and Quality: Advanced scale-up tech leads to consistent product quality. The production PSD will closely match the lab’s PSD, meaning the final products (be it a battery electrode or ceramic part) will perform as intended. This consistency builds confidence in the manufacturing process. It also simplifies regulatory approvals in fields like pharmaceuticals, where you must demonstrate that the full-scale process is equivalent to the lab/pilot process used during development.
- Knowledge Retention and Transfer: Using systematic approaches (like specific energy matching or digital twins) turns scale-up from an “art” into more of a science. The knowledge gained can be documented and reused. If you develop a new oxide powder next time, you can apply the same modeling approach to scale it up. Over time, each successful scale-up becomes a template for future projects, creating an innovation flywheel.
- Resource Efficiency: Beyond time and materials, other resources are saved too. Optimized scale-up often means optimized energy usage – you avoid over-milling or unnecessary processing, which saves electricity and wear on machines. It can also mean needing fewer people-hours monitoring trials. All this contributes to lower cost of production and a greener process (since wasted energy and materials are reduced).
In essence, these technologies de-risk the journey from lab to production. They give companies the confidence to invest in new processes knowing they won’t be stuck in scale-up limbo indefinitely.
Conclusion: From Lab Bench to Factory Floor, Seamlessly
Scaling up wet milling processes no longer needs to be a leap of faith. With the right combination of consistent equipment design, scientific modeling, real-time monitoring, and smart controls, we can achieve near-perfect translation of lab conditions to industrial scale. Powders like advanced ceramics, battery materials, and oxides can thus be manufactured at ton scales with the same particle size distributions that were so carefully optimized in the lab.
The impact of these innovations is profound – products get to market faster, at lower cost, and with reliable quality. Engineers can spend more time innovating and less time troubleshooting scale differences. As the field continues to evolve (with digital twins and AI-driven control on the horizon), the gap between lab bench and factory floor will only shrink further. For anyone working with powder milling, these are exciting times: the once tricky “art” of scale-up is becoming an accessible science, empowering us to turn great lab ideas into successful mass production with unprecedented efficiency.
Source: https://thebulklab.com