Thermal Wrinkling: A Hidden Challenge in EV Battery Anode Production and Its Solutions
Battery anodes for electric vehicles (EVs) are typically mass-produced using the Roll-to-Roll (R2R) process. However, an unexpected and significant hurdle in this continuous manufacturing method is “thermal wrinkling.” Thermal wrinkling refers to the permanent folds that occur in electrode sheets due to thermal-induced deformation, which does not revert upon cooling. Recent research has highlighted this issue, analyzing its root causes and proposing effective mitigation strategies.
When Does Thermal Wrinkling Occur?
Thermal wrinkling primarily occurs in drying ovens when electrode sheets experience rapid or uneven heating. Differential thermal expansion between the copper current collector foil and the coating layer destabilizes web tension, causing irreversible wrinkling and plastic deformation. Specifically, during the drying stage of the R2R process, high and inconsistent oven temperatures cause uneven thermal expansion rates between layers.
This differential expansion generates uneven mechanical stresses across the electrode web, leading to wrinkles forming primarily in the transverse direction. Factors such as inadequate tension control, roller misalignment, non-uniform coating thickness, or abrupt temperature changes exacerbate the severity of thermal wrinkling, emphasizing the need for precisely controlled manufacturing conditions.
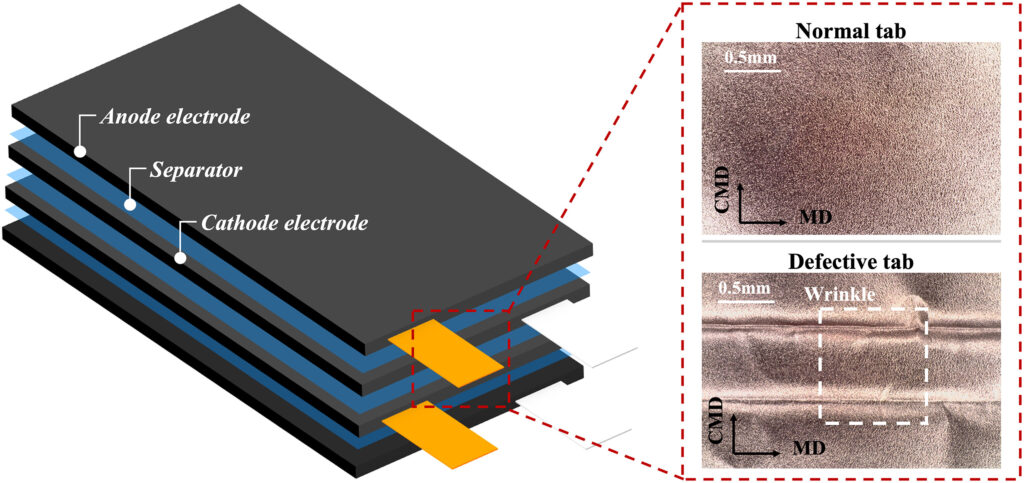
Impact of Thermal Wrinkling
Wrinkled electrodes exhibit compromised flatness and thickness uniformity, directly leading to reduced battery performance and potential safety hazards. Such irregularities may cause localized overheating or minor internal short circuits, resulting in increased defective rates and material wastage. Additionally, uneven electrode surfaces compromise battery stacking accuracy, affecting electrochemical performance consistency and significantly reducing the lifecycle and reliability of battery cells.
Furthermore, manufacturers may resort to conservative drying protocols to mitigate wrinkle formation, resulting in lowered production throughput, increased operational costs, and extended production cycles. These factors highlight the considerable financial and operational repercussions thermal wrinkling imposes on battery manufacturing processes.
Proposed Mitigation Strategies
The research team optimized the drying process temperature profile in detail to effectively mitigate thermal wrinkling. Specifically, they implemented gradual and staged temperature increases within drying ovens and precisely controlled internal airflow to ensure uniform heating conditions. Additionally, to maintain consistent web tension, the team optimized roller placement and employed tension control devices to prevent web sagging. In terms of material design, adjustments to the type and concentration of binders in the coating slurry significantly reduced thermal shrinkage during drying.
In some cases, incorporating nanoparticle-based reinforcements into the coating layer minimized differential thermal expansion and suppressed plastic deformation. Furthermore, thermo-mechanical coupled simulations were used to predict web behavior under various conditions, such as temperature, drying time, and line speed. This proactive approach enabled the identification of optimal operational conditions, significantly reducing experimental trial-and-error efforts. Through these comprehensive strategies, the researchers effectively suppressed thermal wrinkling defects while maintaining productivity, offering a practical and realistic approach for industry implementation.
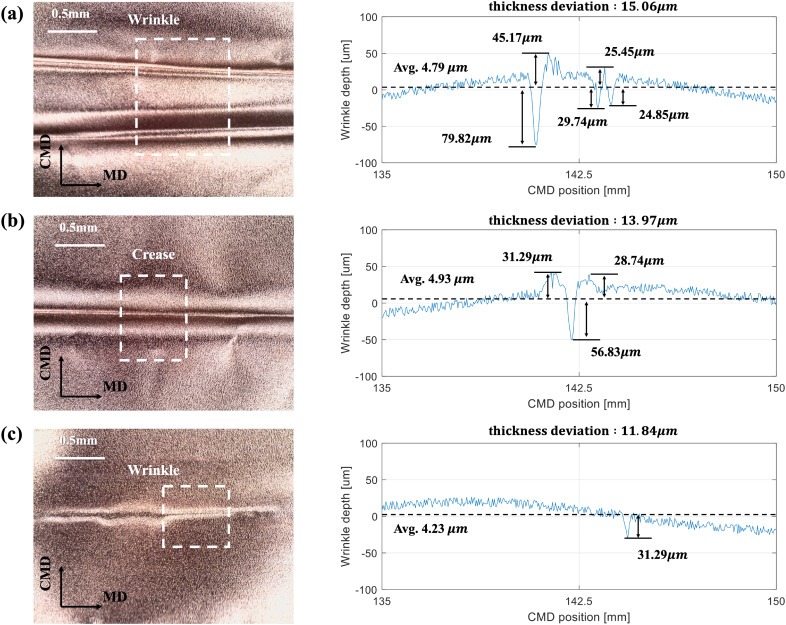
Distinctiveness from Traditional Approaches
Previous methods relied on temporary fixes, such as lowering line speeds, increasing tension, or investing in expensive specialized equipment (rollers or tentering systems). In contrast, this study systematically addresses the root cause, combining process optimization, material improvement, and advanced simulation techniques, offering a practical and comprehensive guideline for wrinkle mitigation without compromising productivity.
Industrial Value and Future Outlook
Addressing thermal wrinkling comprehensively can significantly enhance the overall economic and operational efficiency of battery manufacturing. By mitigating wrinkle-induced defects, manufacturers can notably increase production yields, reduce waste, and achieve more consistent quality outputs. Improved consistency and reliability in battery cell performance directly translate to enhanced battery longevity and safety, bolstering consumer confidence and market competitiveness.
Additionally, optimized production conditions enable higher throughput rates and reduced energy consumption, further decreasing production costs and environmental impact. The methodologies outlined in this research possess broad applicability, extending beyond EV battery anodes to encompass various roll-to-roll processes, including flexible electronics, solar cells, and advanced materials manufacturing. Consequently, these advancements provide substantial strategic value, positioning industries to better meet escalating market demands for higher-quality, cost-effective, and sustainable products.
DOI: https://doi.org/10.1016/j.jmapro.2025.02.069
Source: https://thebulklab.com